As the fall harvest nears and we’re tuning up our equipment, the thought of custom hiring out our harvesting work comes to mind for some. There are many factors to consider as we make custom hire versus ownership decisions, with cost considerations generally at the forefront of our thoughts.
Rates for combining irrigated corn, dryland corn, and soybeans on a per-acre basis from the 2022 Nebraska Custom Rates Survey Report are shown below. The full report is available at: cap.unl.edu/customrates. The custom rates for harvesting fall crops vary across Nebraska due to the variability of crop yields, the type of ground, the availability of custom operators, and the demand for custom services in some areas versus others.
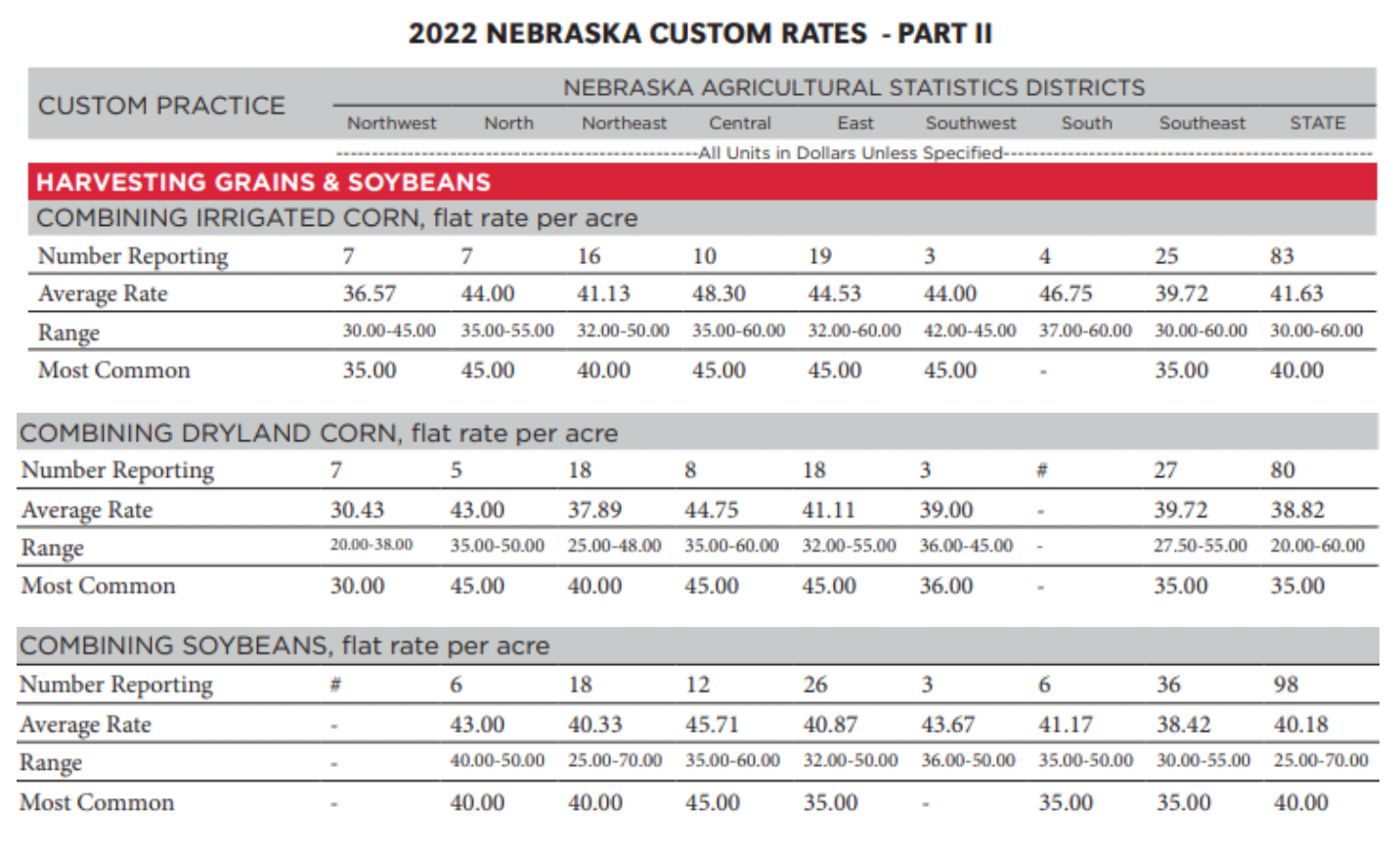
When owning harvest equipment (including the combine, corn head, and grain platform for soybeans and other crops), it is essential to consider ownership costs, including depreciation, interest, taxes, insurance, and housing for equipment. Annual operating costs, including fuel and lubricants, repairs and maintenance, and labor, must be added to ownership costs to get total costs. Remember that machinery prices, interest, insurance, fuel, and labor have most likely increased over the last year and a half since the latest survey.
The Center for Ag Profitability’s (CAP) Agriculture Budget Calculator (ABC) program can be efficiently utilized to determine harvest equipment's field operation costs. Once we have a good handle on costs, we can make comparisons and informed decisions on owning versus hiring custom work to be done.
Agriculture Budget Calculator Program Data Entries for Machine Ownership and Operation Costs
Data needed in the ABC program to figure ownership and operation costs for power units and implements should be readily available. Once list prices of comparable machines, purchase price, age when purchased, purchase price, expected years of ownership, and hours on power units and acres, along with coverage rate on implements, are entered, the program calculates salvage value for depreciation and repairs using American Society of Agricultural and Biological Engineers (ASABE) formulas. Fuel, labor, and opportunity costs of investment are also figured from the provided data.
Screenshot of the information entered in the ABC program for a combine (power unit) example:
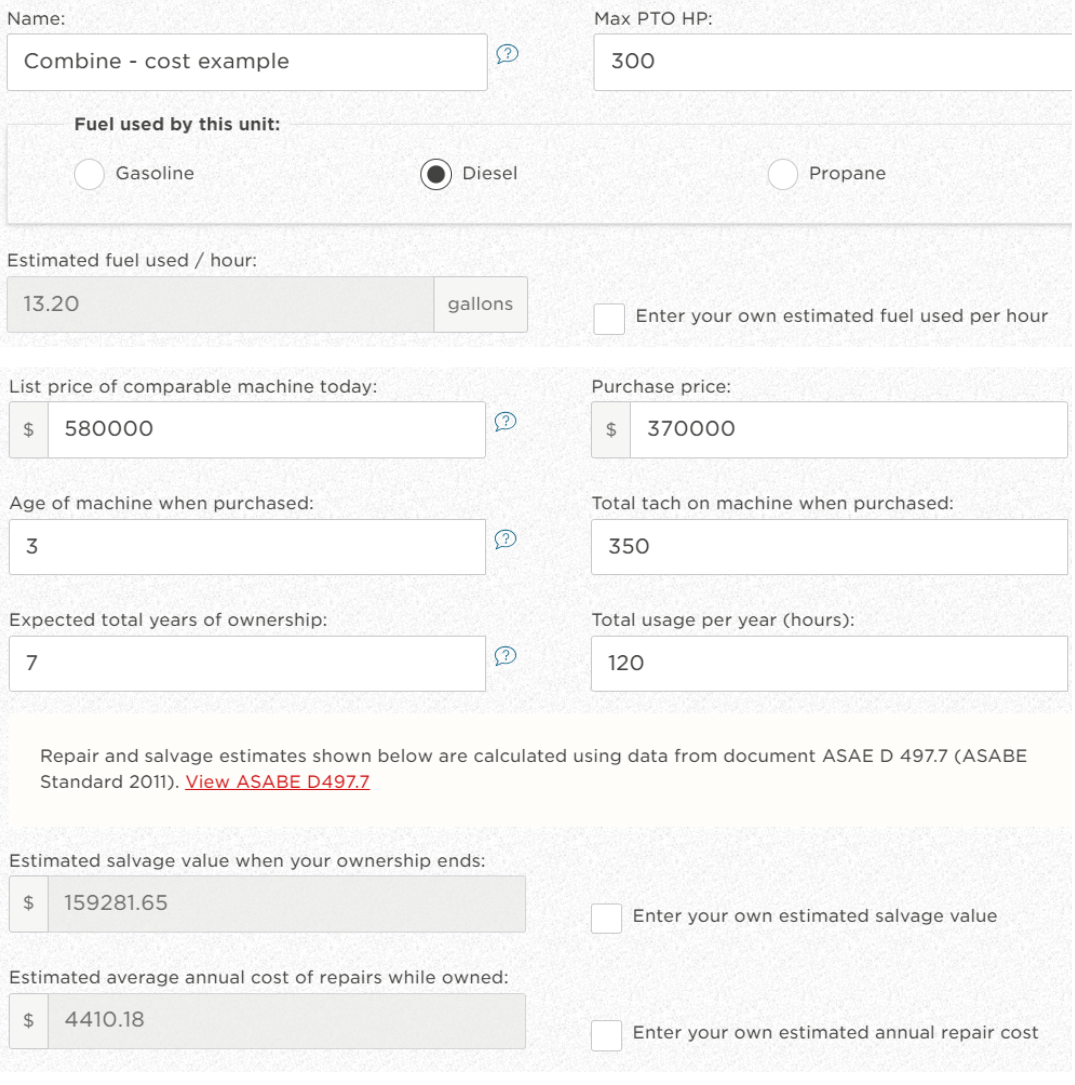
The following screenshot from ABC summarizes the combine (power unit) cost calculations with per-hour cost figures. Once we have the coverage rate from the implement information, costs per acre can be figured.
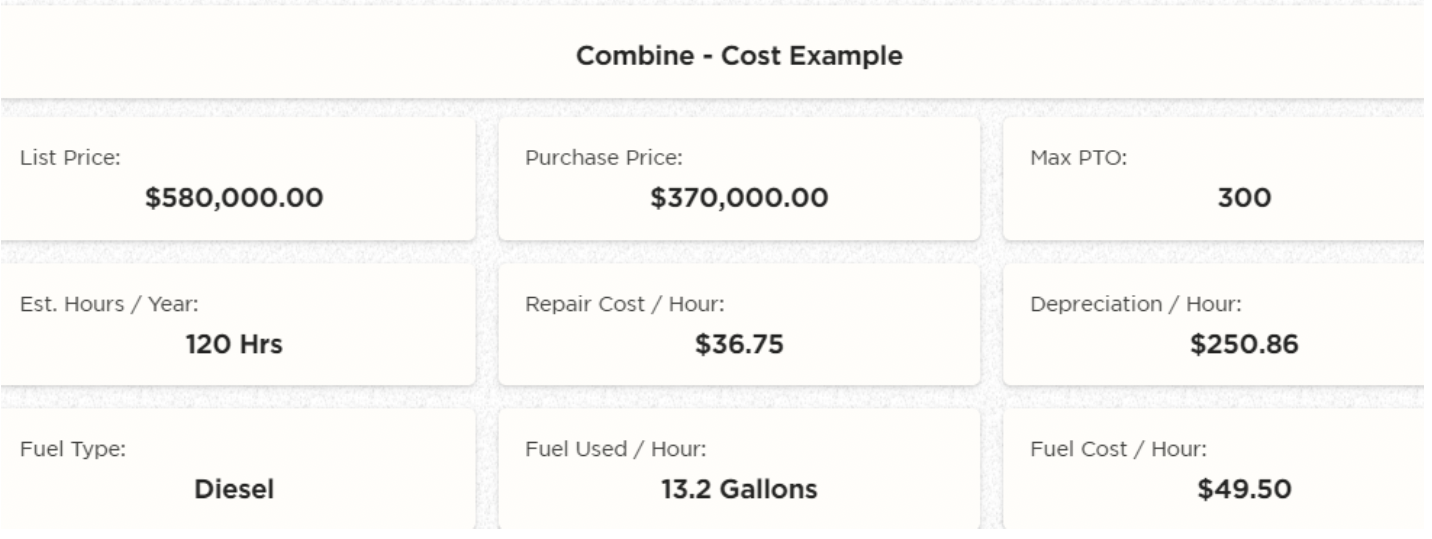
Next, here is a screenshot of the information entered in the ABC program for a combine header (implement) example:
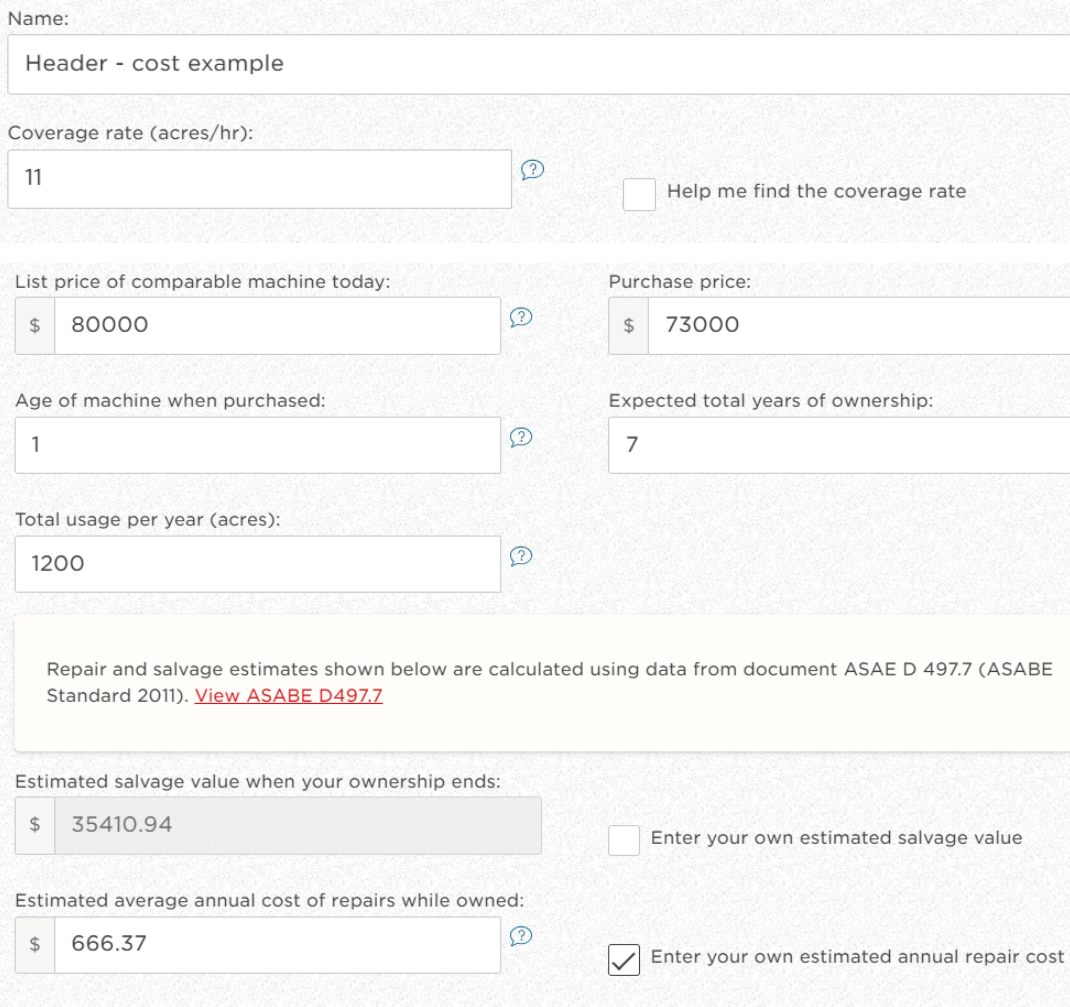
And then, a screenshot from ABC summarizes the header (implement) calculations.
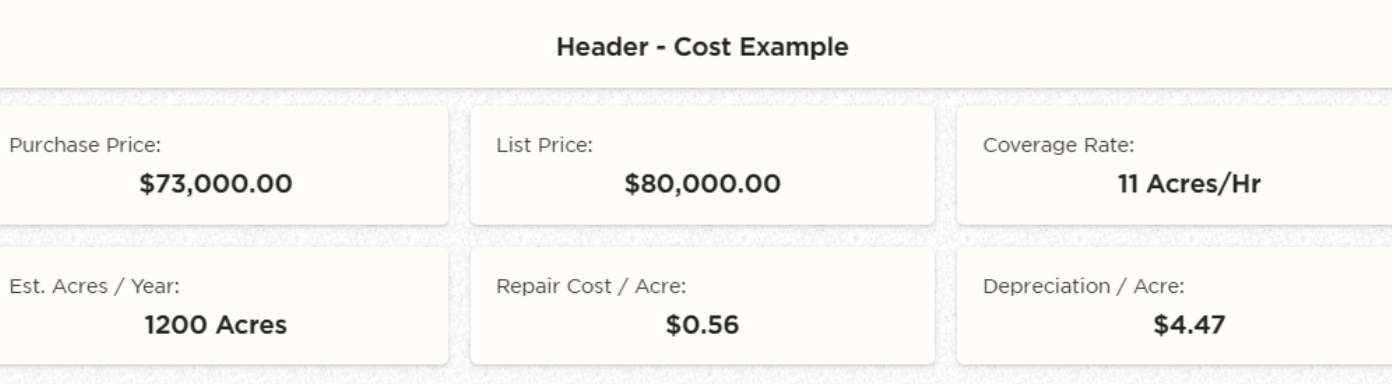
And finally, the combine and header field operation costs are summarized in the following ABC report, showing an estimated $46.41 total cost per acre. This figure can be used to compare what custom operators in the area may be charging.
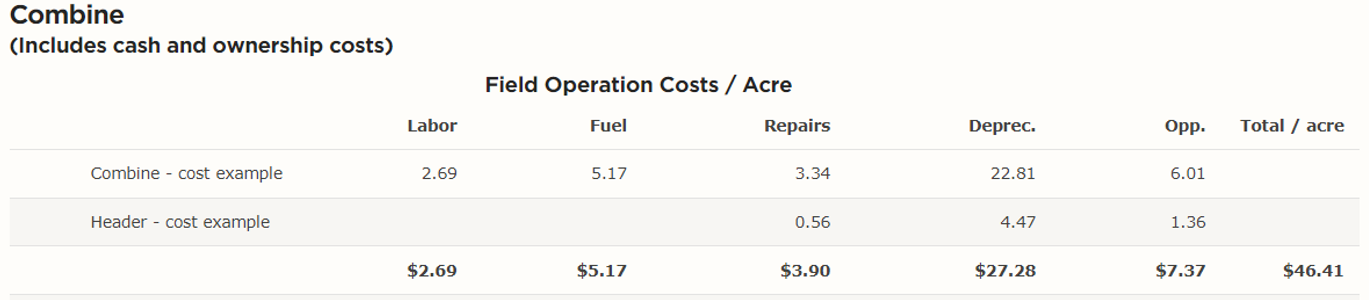
Please note that the machine costs in this report do not include taxes, housing, insurance, or licensing costs. ‘THILM’ expenses may be detailed for your enterprises as cash overhead costs.
In addition to equipment and operational costs, there are other considerations when determining whether to hire field operations and harvesting work done on a custom basis or to own the equipment and do it yourself. The number of acres to be harvested, time, the availability of good custom operators in your area, and harvest efficiency all contribute to making an economic decision.